Sicurezza in magazzino: fattori di rischio, linee guida e soluzioni
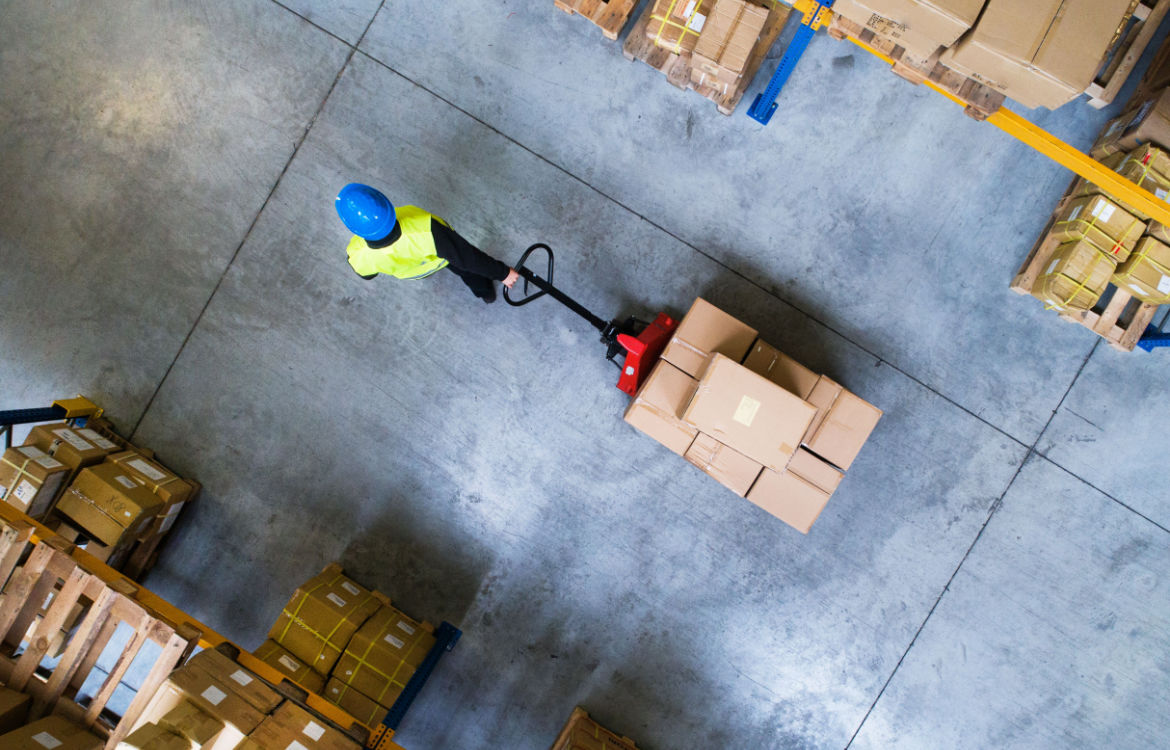
Oggi, la gestione dell’ambiente, della salute e della sicurezza è un impegno univoco sul quale l’azienda deve concentrarsi per migliorare in modo sostenibile le sue prestazioni. La gestione EHS (Environmental Health and Safety – Salute e Sicurezza Ambientale) si riferisce all’implementazione di procedure volte a garantire e migliorare la sicurezza dei lavoratori e dell’ambiente circostante. Per superare queste sfide, l’OSHA (Occupational Safety and Health Administration) ha imposto programmi di gestione EHS. Nel corso degli anni, l’OSHA ha condotto molti studi che dimostrano come l’applicazione dei programmi di gestione EHS hanno contribuito a proteggere il pianeta da diverse minacce ambientali, consentendo allo stesso tempo alle aziende di prosperare e focalizzarsi sul miglioramento dei diritti e della sicurezza dei lavoratori.
Riferimenti europei e italiani
La Commissione Europea ha di recente preso in esame il quadro normativo relativo alla logistica e alla gestione dei magazzini, ritenendolo lacunoso e non adeguato a tenere il passo con l’evoluzione del settore.
La situazione si riflette analogamente anche in Italia, dove le attività svolte all’interno di un magazzino di stoccaggio e distribuzione vengono classificate dalla normativa italiana sulla sicurezza sui luoghi di lavoro come situazioni di rischio medio.
Ricordiamo che i magazzini e, in particolare, le banchine di carico e scarico delle merci, rappresentano le aree potenzialmente più pericolose tra i diversi ambienti logistici.
La tematica è attualmente di grande rilevanza in quanto, per far fronte alle sfide legate all’espansione dell’e-commerce, i grandi operatori della logistica hanno costruito nuovi Hub e grandi magazzini: tipicamente luoghi in cui interagiscono non solo persone, ma anche carrelli, mezzi di movimentazione e macchinari automatizzati. Proprio per queste caratteristiche, i magazzini sono divenuti luoghi ibridi e complessi dove il bisogno di maggiore produttività, efficienza e velocità delle operazioni deve necessariamente coniugarsi con la tutela della safety dei lavoratori. Una tutela che non può prescindere dalla gestione dei tanti aspetti di safety e security legati ai mezzi di movimentazione utilizzati all’interno del magazzino, tra cui: la regolazione di accessi da parte degli operatori a determinate zone della warehouse o dei permessi per utilizzare i mezzi e la gestione dei flussi all’interno del magazzino.
Queste tutele includono anche la prevenzione, la mitigazione dei fattori di rischio che potrebbero portare a collisioni tra mezzi o tra un mezzo e l’operatore, la corretta manutenzione degli asset impiegati: la ragione è insita nell’attività che vi viene svolta e che prevede un movimento continuo di persone e presenza di carrelli elevatori.
Va ricordata, a livello europeo, la normativa ISO 45001, introdotta come standard di riferimento per certificare l’adeguatezza dei Sistemi di Gestione per la Salute e la Sicurezza sul Lavoro, in sostituzione alla normativa britannica OHSAS.
La sicurezza in magazzino secondo la normativa italiana
In Italia, sono presenti un numero elevato di leggi in materia di sicurezza sul lavoro, questo perché la salute è definita dalla Costituzione Italiana come un diritto fondamentale: è quindi indispensabile tutelarla in tutti gli aspetti, anche sul posto di lavoro.
La prima fonte normativa di cui tenere conto è il Codice Civile. In quest’ultimo si sottolinea l’importanza di garantire sicurezza sul luogo di lavoro e, in particolare, le responsabilità del datore di lavoro, attribuendo ad esso l’incarico di adottare tutte le misure idonee a prevenire sia i rischi insiti all’ambiente di lavoro, sia quelli esterni derivanti dall’ambiente circostante (definiti rischi da interferenza).
Una seconda fonte normativa, che entra più nel dettaglio tecnico della disciplina, è rappresentata da uno dei decreti più importanti in termini di salute e sicurezza: il Decreto Legislativo 81/2008, detto anche Testo Unico sulla Sicurezza o altrimenti conosciuto con l’acronimo TUS o TUSL (Testo Unico sulla Sicurezza nei Luoghi di Lavoro). Approvato attraverso Decreto Legislativo il 9 aprile 2008, il TUS raccoglie un complesso di norme che disciplinano la sicurezza sul luogo di lavoro.
La normativa dei magazzini
La semplice definizione di “magazzinaggio”, così come riportata dalle normative (Accordi Stato Regione 2011), è alquanto riduttiva e non tiene conto delle numerose ed eterogenee realtà che in questo termine possono essere comprese.
La valutazione del rischio e della sicurezza all’interno di un magazzino rientra tra gli obblighi del Datore di Lavoro e deve partire necessariamente dal contesto lavorativo in cui è inserito il magazzino, considerando diverse variabili come, ad esempio, i livelli di automazione presenti, la quantità di personale impiegato, la presenza di prodotti pericolosi e l’utilizzo dei luoghi di lavoro.
I possibili fattori di rischio a cui è esposto il personale che presta la sua opera nella gestione del magazzino, sono relativi a tre diverse macrocategorie:
- rischi connessi al luogo di lavoro
- rischi connessi alle attrezzature utilizzate
- rischi per la salute del personale
L’importanza del tema sulla sicurezza dei luoghi di lavoro ha spinto le aziende ad andare oltre ai semplici doveri normativi, sviluppando dei sistemi di gestione dei rischi sulla base di linee guida e norme volontarie. Quando si parla di Sistema di Gestione della Sicurezza sul Lavoro (SGSL) si fa riferimento ad un sistema organizzativo interno all’azienda, finalizzato a garantire il raggiungimento degli obiettivi di salute e sicurezza sul lavoro attraverso la massimizzazione dei benefici e la riduzione dei costi. Con un SGSL, la gestione della sicurezza e salute nel magazzino diventa parte integrante della gestione complessiva dell’azienda.
Oltre alla normativa
Alla base della sicurezza in magazzino vi è certamente il suo lay-out da progettare, mettendo a punto una migliore organizzazione del lavoro, in maniera che i percorsi dei veicoli, lo spostamento delle merci e gli itinerari a piedi avvengano senza essere di reciproco intralcio.
Tuttavia, i rischi relativi dipendono non solo da come i mezzi di movimentazione circolano all’interno del magazzino, ma anche da quanto è adeguata la capacità di guida dei mezzi da parte del conducente. Molti degli incidenti che ancora oggi si registrano nei magazzini sono infatti dovuti a competenze non adeguate nell’utilizzo dei mezzi impiegati o, addirittura, all’utilizzo di mezzi per cui non si possiede la licenza necessaria. Ecco perché l’ammodernamento degli asset impiegati nel magazzino – sia per quanto riguarda l’hardware che i software – deve procedere di pari passo con la formazione del personale.
Fornire mezzi dotati dei più avanzati dispositivi tecnologici, un training costante volto a tenere alta la consapevolezza dei rischi, la manutenzione effettuata con regolarità e l’accesso limitato alla guida delle macchine solo a chi possiede le necessarie competenze sono tra i fattori che contribuiscono a rendere i luoghi di lavoro più sicuri.
Rischi e prevenzione: il contributo di Ubiquicom
Ubiquicom, sviluppa prodotti e soluzioni per la localizzazione ed il tracking in tempo reale, avvalendosi delle più avanzate tecnologie RTLS (Real-Time Locating Systems) e di sensoristica diffusa.
Grazie all’esperienza maturata negli anni, Ubiquicom ha riconosciuto il carrello elevatore come protagonista dei processi logistici e di magazzino, mettendolo al centro di un ecosistema di soluzioni in grado di portare safety & efficiency ai massimi livelli: Forklift Ecosystem.
All’interno di questo ecosistema hanno particolare rilevanza i sistemi di anticollisione carrello-carrello e carrello-pedone, rilevamento e allarme di situazione di uomo a terra, zoning, permessi di guida, controllo accessi e reportistica in grado di analizzare situazioni di near miss per il miglioramento del lay-out di magazzino ai fini della sicurezza.
Con riferimento in particolare a situazioni di trasporti complessi, come negli Hub precedentemente evidenziati, Ubiquicom propone soluzioni di anticollisione avanzate, basate su strumenti di localizzazione in tempo reale ad alta accuratezza e con tecnologia UWB (Ultra WideBand). Forte della sua esperienza in questo campo, Ubiquicom può anche sviluppare progetti personalizzati sulle esigenze e al particolare contesto in cui operano i clienti, così da sfruttare il potenziale offerto dalle tecnologie per incrementare la safety all’interno del magazzino, senza compromettere l’efficienza dei processi operativi.
Un interessante customer case in ambiente logistico ha riguardato un’azienda leader nel settore delle consegne espresse, che aveva l’esigenza di prevenire le collisioni uomo-macchina e macchina-macchina, oltre all’obiettivo più generale e complesso di ridurre i fattori di rischio presenti all’interno del magazzino e di incrementare la safety. Ubiquicom ha saputo rispondere a queste necessità grazie a una suite di sistemi anticollisione ad elevata precisione basati sulla localizzazione in tempo reale di mezzi e personale. I sistemi si basano, a seconda della precisione e della accuratezza, su dispositivi hardware:
- Gli operatori sono stati dotati di Tag persona
- I carrelli e i mezzi di movimentazione sono stati equipaggiati con il Kit radar di Ubiquicom
- Gli ostacoli fissi presenti all’interno del magazzino sono segnalati con radar o antenne speciali (ancore)
La sicurezza dei lavoratori è abilitata da segnali di allarme (suoni e vibrazioni) che si attivano automaticamente in condizione di vicinanza pericolosa tra mezzo e operatore o tra due mezzi, anche in situazioni di angolo cieco. I sistemi, inoltre, permettono di regolare l’accesso ad aree del magazzino che sono considerate a rischio.
I vantaggi che ne derivano in ottica di sicurezza in magazzino sono molteplici: la riduzione degli infortuni e di incidenti durante le attività lavorative, la diminuzione dei costi di manutenzione delle infrastrutture danneggiate dai carrelli e l’aumento della sicurezza reale e percepita, con una conseguente serenità dei lavoratori.
Di particolare interesse sono i sistemi di controllo delle zone e i sistemi anticollisione coadiuvati da dispositivi che rallentano i carrelli esclusivamente in situazioni che necessitano maggior cautela. La sensoristica a bordo del carrello è pensata per la riduzione degli incidenti, che possono avvenire muovendosi tra i corridoi dei magazzini con la velocità richiesta dagli elevati ritmi delle moderne supply chain.
Le Tag di Ubiquicom, infatti, permettono di prevenire gli incidenti e ridurre l’impatto che questi potrebbero avere sull’azienda. Con le soluzioni di safety di Ubiquicom si possono inoltre associare informazioni sul personale – raccolte nel pieno rispetto della privacy dei lavoratori e delle normative vigenti – e sapere se chi guida il carrello ha la patente e le qualifiche per farlo.
Le soluzioni di Ubiquicom sono applicabili in vari settori: nella logistica, nel manufacturing, nei trasporti e nella sanità.
Forklift Ecosystem è l’ecosistema completo e integrato caratterizzato da 5 aree: telematica con TRACKVISION, anticollisione (Safety) con la gamma PROXIMITY, RTLS con LOCATOR, Intelligenza Artificiale con SYNCHRO, diagnostica da remoto con SHINDAN.
TRACKVISION è il sistema di gestione del parco mezzi di movimentazione in ottica 4.0. Abilita la telemetria, la localizzazione, la sicurezza e la diagnostica remota su veicoli per la movimentazione delle merci e asset motorizzati.
Anticollisione con la gamma PROXIMITY. Tutte le soluzioni anticollisione sono in grado di effettuare il rallentamento automatico del veicolo e la segnalazione luminosa e acustica, sono basate sulle più moderne tecnologie di localizzazione in tempo reale, per misurare con la massima precisione le variabili su cui i sistemi si basano per riconoscere le situazioni di allerta e quelle di allarme. PROXIMITY è il sistema anticollisione basato sulla posizione relativa del carrello con a bordo il Kit Radar PROXIMITY e il pedone con Tag persona al braccio, che genera una “bolla di sicurezza”.
PROXIMITY PLUS è un sistema anticollisione sofisticato che, grazie al Kit Radar PROXIMITY a 3 o più antenne, è in grado di determinare la possibile collisione con i pedoni identificando la traiettoria e la posizione sul visore a bordo carrello. L’area di sicurezza intorno al carrello viene determinata via software e cambia forma a seconda della velocità e delle condizioni operative, in modo da limitare al massimo i falsi allarmi che riducono la produttività.
THIRD EYE è studiato per garantire contemporaneamente i più avanzati livelli di Sicurezza ed Efficienza, grazie alla tecnologia AOA e al calcolo dinamico della traiettoria: risultati tangibili sono il miglioramento della prevenzione di urti e incidenti, e contemporaneamente la generazione di allarmi solo in condizione di reale pericolo di collisione. THIRD EYE è indicato per tutti i tipi di mezzi, dai veicoli industriali e logistici ai macchinari pesanti ed è la soluzione ideale per tutti quegli ambienti complessi in cui è più elevato il rischio di incidenti o urti tra mezzi, operatori a piedi e ostacoli fissi.
La gamma PROXIMITY risponde a ogni esigenza di sicurezza, dalla più basilare a quella più sofisticata, coinvolgendo persone e mezzi di movimentazione, compresa l’integrazione con il software SAFETY LOCATOR. Grazie a questo software è possibile conoscere la localizzazione in tempo reale dei carrelli, aggiungendo funzionalità come la rilevazione dell’uomo a terra e lo zoning per rallentare i carrelli nelle aree a maggior rischio, anche in base alle fasce orarie in cui la presenza di pedoni è più o meno intensa a seconda dei turni di lavoro.