L’evoluzione dei sistemi di localizzazione intralogistica: RTLS vs RFID
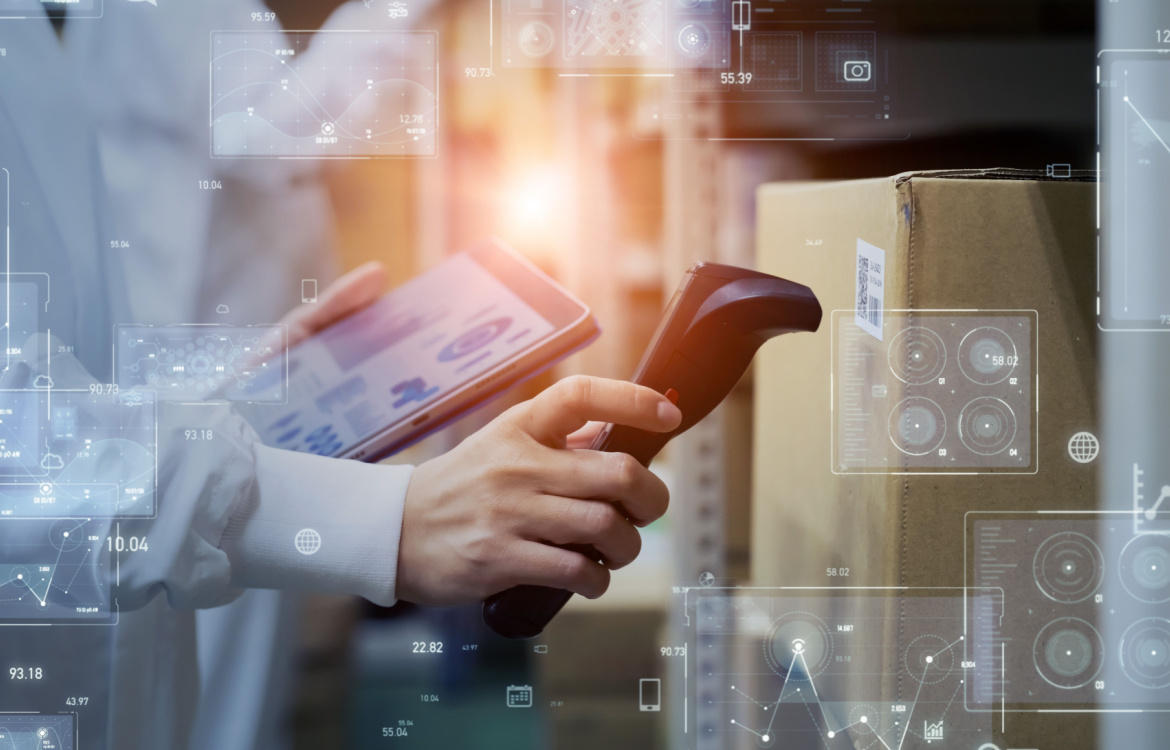
Nelle moderne smart factory, Industry 4.0 è sinonimo di efficienza e produttività nella misura in cui ogni processo, grazie all’acquisizione e all’analisi dei dati, viene identificato, tracciato e ottimizzato. Questo è ancor più vero nel comparto dell’intralogistica, dove il tracciamento degli asset e la localizzazione in tempo reale di personale, merci e risorse, influiscono in modo determinante sia sulla produzione, sia sul funzionamento complessivo dello stabilimento. Proprio grazie ai dati che possono essere ricavati tramite sistemi RFID (Radio-Frequency IDentification) e RTLS (Real-Time Locating Systems), le aziende riescono a porre le basi per un’intralogistica ottimizzata in cui flussi di movimentazione di merci, mezzi e persone all’interno dello spazio di lavoro divengono più fluidi, efficienti e sicuri, garantendo maggiore competitività in mercati caratterizzati da una domanda mutevole e costi di produzione elevati.
I sistemi di localizzazione applicati all’intralogistica offrono numerosi vantaggi per la gestione di magazzino, aumentandone produttività ed efficienza e migliorandone quindi le prestazioni. Dalla visibilità in tempo reale dell’inventario, che porta a minori costi di stoccaggio e migliore reattività ai cambiamenti della domanda del mercato, e dall’ottimizzazione dello spazio all’indicazione del percorso più efficiente da seguire, fino al miglioramento della sicurezza sul posto di lavoro – con la prevenzione degli incidenti causati da collisioni tra lavoratori e veicoli in movimento –, questi sistemi coniugano l’incremento dell’efficienza con quello della sicurezza.
L’evoluzione dei sistemi di localizzazione intralogistica
Il tracciamento, per una intralogistica efficiente e sicura, si basa principalmente su due tipologie di soluzioni: i sistemi di localizzazione in tempo reale (RTLS, Real-Time Locating Systems) e quelli di identificazione a radiofrequenza (RFID, Radio-Frequency IDentification).
I primi si basano tipicamente su dispositivi attivi e piattaforme software per la localizzazione e il tracciamento e consentono di conoscere, in tempo reale, la posizione fisica di operatori, asset, attrezzature e mezzi per la movimentazione. In funzione dell’accuratezza richiesta e dell’ambito di applicazione, questi sistemi possono basarsi su diverse tecnologie: dall’Ultra WideBand (UWB) al BLE (Bluetooth Low Energy), fino ai sistemi GNSS e a quelli ottici. I tag RFID sono tradizionalmente considerati l’evoluzione dei barcode e consentono di identificare in modo rapido e automatico la merce mediante letture puntuali grazie alle quali è possibile avere una visione sempre aggiornata, ad esempio, delle disponibilità di semilavorati e prodotti finiti in magazzino e implementare la tracciabilità completa dei prodotti.
Esistono diverse tipologie di tag RFID, ma possiamo innanzitutto distinguere:
- Tag RFID passivi: si basano su microchip, antenna e substrato e sono privi di alimentazione. Per poter trasmettere le informazioni, questi tag devono essere attivati da un reader, mediante l’emissione di un segnale radio che fornisce al tag stesso l’energia per funzionare e trasmettere il proprio identificativo;
- Tag RFID attivi: questo tipo di tag, oltre a microchip, antenna e substrato, è dotato di alimentazione propria che consente al tag di trasmettere a distanze sensibilmente superiori
L’evoluzione dei Real-Time Locating Systems è trainata dalla crescita del mercato globale della tecnologia UWB, che nel 2022 ha generato entrate per circa 1 miliardo di dollari. Un report di Research Nester stima, infatti, che il mercato globale della tecnologia a banda ultra larga (UWB) genererà entrate per circa 5 miliardi di dollari entro la fine del 2033, crescendo a un CAGR del 20% nel periodo di previsione 2023-2033.
RTLS vs RFID: le differenze fra le due soluzioni per l’intralogistica
Va innanzitutto premesso che i due sistemi – RFID e RTLS – non devono essere visti come alternativi, ma, al contrario, come complementari. Dalla sinergia di identificazione automatica (RFID) e localizzazione (RTLS), seguendo un approccio data-driven, si può arrivare infatti all’implementazione di soluzioni che coniugano economicità ed affidabilità per generare ROI signifcativi.
Per ragioni di crescita e di diffusione, possiamo ragionare dei sistemi RTLS partendo dalla tecnologia UWB, ma discorsi analoghi potrebbero essere fatti per le altre tecnologie radio utilizzate nella localizzazione. La tecnologia Ultra WideBand (UWB) offre elevata precisione, tempi di aggiornamento brevissimi e, in generale, la possibilità di applicazione a differenti scenari quali la localizzazione di merci, persone, strumenti, veicoli e contenitori.
Dal punto di vista puramente tecnologico, RFID e UWB si differenziano innanzitutto per le bande utilizzate:
- le tecnologie RFID operano in banda LF (Low Frequencies – 125-134 kHz), HF (High Frequencies – 13,56 kHz) e UHF (Ultra High Frequency – 865-928 MHz) e consentono di raggiungere distanze di lettura fino ad alcuni metri;
- i sistemi RTLS basati su UWB lavorano invece a frequenze più elevate e operano a una larghezza di banda molto ampia (3,1- -8,5 GHz), e consentono distanze di comunicazione molto più elevate.
L’altra differenza fondamentale tra le due tecnologie riguarda le modalità di alimentazione del dispositivo radio. I tag RFID sono normalmente alimentati a induzione, privi di batteria e si attivano solo quando si trovano nel raggio di azione di un lettore RFID. I tag UWB invece sono sempre “attivi”, alimentati cioè a batteria, e trasmettono un segnale identificativo a intervalli regolari o secondo logiche definite in base al progetto specifico.
In virtù di queste differenze tecnologiche, l’RFID trova quindi una migliore applicazione nell’identificazione veloce e automatica di asset attraverso l’utilizzo di reader grado di leggerne la presenza: nelle movimentazioni dell’intralogistica, grazie ai tag RFID, è possibile individuare con precisione l’unità di carico che viene movimentata o, anche, l’elenco dei singoli prodotti presenti su un pallet fornendo così l’informazione a sistemi gestionali di magazzino ed, eventualmente, alla piattaforma di localizzazione.
D’altra parte, la tecnologia UWB trova applicazione efficace nella localizzazione accurata consentendo, ad esempio, di conoscere con precisione la posizione in cui un carrello elevatore ha depositato un pallet o quella in cui si trova un rack di componenti per il rifornimento delle linee.
In un ambiente di fabbrica che prevede l’utilizzo di isole autonome che operano sui manufatti e nella localizzazione di veicoli, persone o prodotti, i sistemi basati sulla tecnologia Ultra WideBand consentono una migliore definizione non solo della posizione dell’oggetto, ma anche della direzione dei suoi spostamenti in tempo reale.
Localizzazione indiretta nell’intralogistica: le soluzioni di Ubiquicom
Una maggiore visibilità sulla posizione degli asset permette, dunque, di ottimizzare i tempi dell’intralogistica e impiegare i mezzi in modo più sicuro ed efficiente.
A questi obiettivi punta l’offerta di Ubiquicom, che ruota intorno alla piattaforma Locator per la localizzazione in tempo reale, il tracciamento di persone, veicoli e asset, la telemetria e la gestione real-time di eventi complessi incentrati sulla posizione.
Utilizzando architetture e protocolli standard, uno dei punti di forza della piattaforma Locator è la capacità di comunicare in modo bidirezionale con diverse tipologie di dispositivi e, processando i dati di campo generati da molteplici tecnologie di localizzazione, di calcolare la posizione di ogni oggetto monitorato, eseguire attuazioni e generare eventi basati sulla posizione, mettendo a disposizione di altri strumenti software tutti i dati di posizione storici e real-time. Ubiquicom Locator è l’unica piattaforma di localizzazione completamente indipendente dalla tecnologia e dai dispositivi utilizzati.
La soluzione Real-Time Locating System (RTLS) di Ubiquicom per la protezione e la sicurezza dei lavoratori è Safety Locator Suite, con la quale, oltre alla posizione di persone e mezzi all’interno dell’area di lavoro, tramite dispositivi attivi vengono rilevati e analizzati in tempo reale numerosi dati per identificare situazioni di rischio o di incidente.
Con l’opportuno mix hardware-software richiesto dal singolo scenario, la piattaforma è in grado di gestire diversi aspetti, tra i quali anche i rischi di collisione con mezzi di lavoro e gli eventi di uomo-a-terra o di urto, le richieste di soccorso o i processi di evacuazione di un’area.
Nell’ambito della sicurezza, un sistema RTLS come Ubiquicom Locator permette anche di ottenere un maggiore controllo sull’operatività e sui comportamenti del personale al fine di migliorarne le condizioni di sicurezza.
Intralogistica: la soluzione di Ubiquicom per la localizzazione indiretta di semilavorati e prodotti finiti
Avere un quadro chiaro e costante dell’esatta posizione e l’avanzamento sulla linea di produzione di ogni semilavorato e dei lotti di prodotto finito all’interno di un magazzino, è un fattore determinante per migliorare l’efficienza dell’intralogistica aziendale e per l’organizzazione della successione dei processi nelle tempistiche stimate. La gestione automatizzata del ciclo produttivo e la completa tracciabilità di tutti i materiali utilizzati, infatti, garantisce un controllo totale sui processi.
La soluzione di localizzazione indiretta predisposta da Ubiquicom si basa sul tracking tramite tecnologia Ultra WideBand dei carrelli elevatori e sull’utilizzo della tecnologia RFID per l’identificazione automatica dell’unità di carico trasportata.
I carrelli elevatori vengono equipaggiati con una o più tag UWB montate sul tetto e alimentate direttamente dalla batteria del carrello, e con un lettore RFID montato sulle forche tramite cui identificare automaticamente l’unità di carico trasportata senza scendere dal mezzo. Le unità di carico vengono etichettate con tag RFID passivi sui due lati di inforcamento.
Grazie alla soluzione Ubiquicom Locator, è possibile conoscere in tempo reale la posizione dei carrelli e la collocazione delle unità di carico, aggiornata in tempo reale nella base dati dal momento del prelievo fino al momento dello scarico, salvando le coordinate a partire da quelle del carrello elevatore.
Il vantaggio è che la posizione dei semilavorati e dei prodotti finiti non è più aggiornata manualmente, ma è sempre disponibile a sistema. In più, per ogni prodotto finito è possibile ricostruire con esattezza tutte le fasi della lavorazione, le macchine utilizzate, l’orario di completamento di ogni lavorazione e i tempi totali di produzione visualizzando su mappa il percorso seguito dal prodotto.
Utilizzando la piattaforma Locator è inoltre possibile conoscere sempre in tempo reale la posizione di ogni carrello elevatore e generare report storici sui flussi e sull’utilizzo delle risorse.
Ubiquicom segue direttamente il setup del software, l’integrazione con gli altri componenti software, la configurazione delle mappe e la messa in opera presso lo stabilimento del cliente e supporta il cliente e i suoi fornitori per l’installazione delle antenne fisse e l’equipaggiamento dei carrelli.
Localizzazione indiretta delle merci indoor e outdoor con carroponte, cavalieri e muletti nelle acciaierie
Un’altra applicazione interessante per la localizzazione indiretta delle merci riguarda in particolare le aziende del settore acciaio e della trasformazione di semilavorati di acciaio (coil, lastre, tubi, barre) che dispongono di magazzini di grandi dimensioni sia al coperto sia in grandi piazzali, dove vengono stoccati (disposti in cataste, anche su più livelli) i semilavorati etichettati con codici a barre o etichette RFID.
Per l’intralogistica e la logistica in uscita, la movimentazione avviene con carriponte, mezzi speciali detti cavalieri e muletti particolari. Per eseguire lavorazioni intermedie e per aumentare il numero di spedizioni giornaliere, l’esigenza è quella di ridurre i tempi di ricerca dei semilavorati e dei prodotti finiti.
Con la localizzazione indiretta, attraverso la conoscenza della posizione del carroponte e dei muletti (compreso l’asse zeta), è possibile identificare costantemente momento e luogo esatto del carico/scarico e avere in tempo reale l’inventario per tipologia di merce, quantità e posizione.
Grazie a questa tecnologia, vengono inoltre ridotte sensibilmente le spedizioni errate, con benefici importanti del livello di servizio ai clienti.
Vuoi saperne di più?
Compila il form, un nostro consulente ti contatterà per darti maggiori informazioni.