RTLS: 3 benefits for intensive logistics
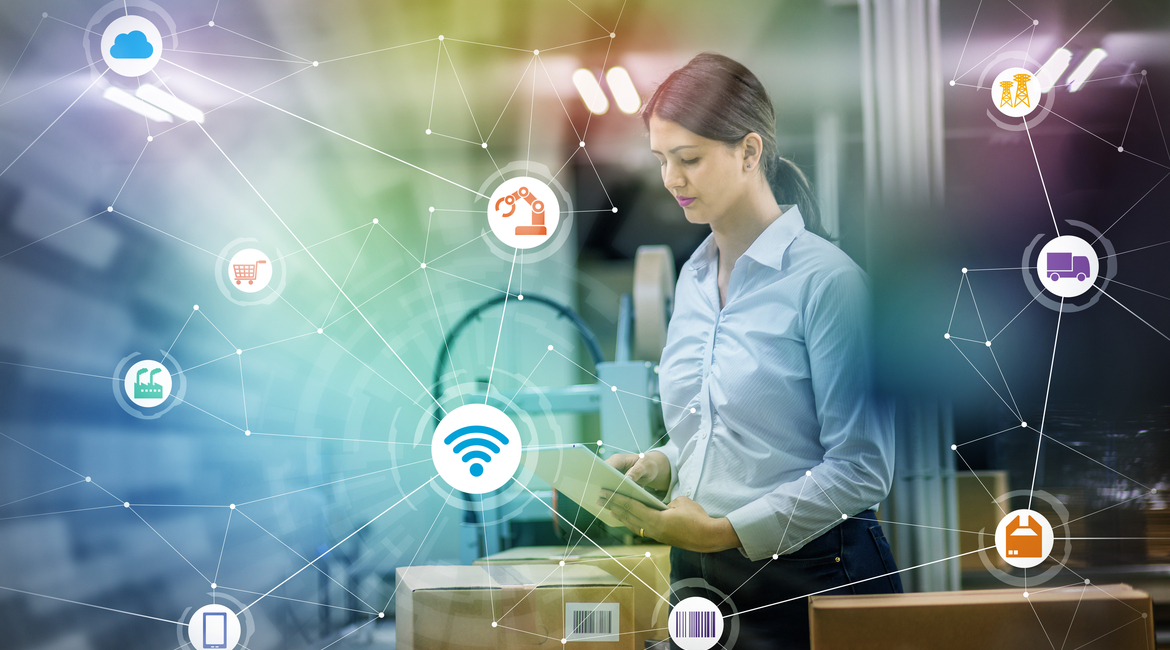
Under several circumstances, it is necessary for a company to adopt intensive logistics solutions. The causes can be many: the most common one refers to the need to increase storage capacity, as well as the number of pallets to be handled in the warehouse. This need often arises from the desire to find an effective way to optimize available spaces inside the warehouse and avoid expensive slowdowns, caused by the difficulty of tracing the products meant to be handled.
It should be remembered that the term “warehouse” refers to that logistics structure able to receive goods, store them and make them available for sorting, shipping and delivery. The storage capacity of a warehouse moves along the delicate balance between available space and productivity. Every centimeter of a surface is valuable: for this reason, an empty space in a facility is always synonymous with waste. In the same way, however, the overload of a warehouse could saturate it and complicate operational phases.
RTLS: more efficiency in intensive warehouses
If we believe that stock growth is a lasting phenomenon, able to cover a time span of many years, it could certainly be a solution to try and expand or multiply warehouses. If, however, the overflow phenomenon is to be considered concerning, for example, in regards to seasonal peaks, substantial investments in the expansion of surfaces and/or heights of infrastructures are not always meant to be justified.
Leaner solutions lead, instead, to think of growth on and within oneself or, more accurately, of realisation of interventions with non-invasive modification projects of current layouts in order to rebalance the SUC (Soil Use Coefficient measured in plt/sqm) towards higher values. In some cases, it’s about doubling and, sometimes, even tripling the SUC. It follows, then, a consequent growth of the receptive potential of stock areas without the need to increase their extent. Simply, one operates by making a better use of the storage characteristics of the same area, enhancing the traceability of stored products.
Therefore, intensive warehouses are a good answer to this need. On the other hand, it must be said that this storage solution often has low selectivity and in some cases does not allow any FIFO (First in first Out) logic to be applied: this happens since, in order to extract pallets located in the innermost position of a structure, it is necessary to withdraw those that precede them.
To know what, where and when, in real time, especially in an intensive warehouse, is the dream of those who have to deal with the management of a warehouse and orders. Over time, supporting technologies have evolved, moving from passive tracking systems to increasingly active and connected methods.
The themes of real-time locating and their application in the field of logistics have long been the focus of interest for every Warehouse Manager, who tries to understand what it’s all about and how to implement these elements to optimize their facility. Real-Time Locating Systems (RTLS), real-time tracking systems, represent the answer to these needs.
RTLS, what they are and how they work
The term Real-Time Locating System translates to a georeferencing system that allows to locate in real-goods and resources, for example, in a warehouse. The most exploited technologies in this logic divide into two main types. Depending on the application area there can be:
- GPS (Geo Positioning System), which mostly exploits satellite technologies and ensures high performance in outdoor environments, even those with significant dimensions;
- IPS (Internal Positioning System), which, thanks to various technologies (including camera, laser, wi-fi, UWB, beacon) can accurately detect a position in indoor environments.
Even if the technological evolution offers new solutions, there are basically two systems to rely on when it comes to traceability: Real-Time Locating Systems (RTLS) and Radio Frequency Systems (RFID, Radio-Frequency IDentification).
These are not mutually exclusive but they are complementary to each other: if the former ones, thanks to geolocation, allow to locate the goods in real time, the latter ones – which are an evolution of barcodes – allow to quantify the goods (for example, to detect which and how many products have been loaded on a truck). It is, therefore, a real data-driven approach: knowing the point in the supply chain where delays and inefficiencies accumulate allows timely interventions, aimed at their resolution.
For example, if through the use of RTLS systems companies and warehouse managers can know in real time the exact location of all resources, their condition and quantity, it is possible to further improve their accuracy by introducing UWB systems (Ultra Wide Band). The latter ones allow sensors to be used in strategic points of a warehouse, giving the possibility to identify the exact coordinates where people, goods, and machinery are located, and to know their movements, consumptions and routes at any time.
RTLS, the 3 main benefits
The RTLS reverse the traditional dynamic of inventory: basically, instead of a human worker meant to search for the goods, it is precisely the latter ones that can give information about what and where they are. This is a particularly strategic benefit since it leads to what is the fundamental cornerstone of this system: having real-time awareness of inventory and at the same time knowing where the goods are placed.
This opens a new frontier of innovation that allows accurate and real-time control of flows within a warehouse, offering the possibility not only to monitor, but also to improve performance thanks to traceability. Through the use of these systems, it is clear how it is possible to use the data collected to:
- reduce the total operating cost;
- improve performance;
- make product traceability more efficient.
6 intensive logistics situations that allow the maximum performance of RTLS
There are certain conditions that allow to maximize the effectiveness of RTLS systems and achieve significant returns on investments. In the specific case, the adoption of RTLS systems is a particularly suitable choice, for example, for those companies that handle material through carts or other vehicles.
There’s more. Taking into consideration handling volumes, a Real-Time Locating System allows to achieve good results in the following cases:
- high handling volumes, even at low stock;
- low handling volumes, but high stock levels;
- a combination of significant volumes, both in handling and stock operations.
Systems of this type are also effective for those companies that need to manage a large number of references and need a traceability system that can eliminate errors. In regards to the last case, but not least, RTLS support those companies that move goods in Units (benches, pallets, crates, stands, big-bags, sacks).
RTLS, AI and WMS: benefits of integration
Additional benefits in intensive logistics come from the use of software combining locating systems and highly performing artificial intelligence (AI) algorithms. For example, thanks to AI, it is possible to create a virtual model of a warehouse, which allows to estimate routes and travel times, optimizing the planning of tasks. With the advantage of the tracking of vehicles, the software analyzes, in real time, the progress of tasks compared to planned operational activities. In this way, it is possible to locate any bottlenecks and modify execution sequences. This allows to optimize the use of material handling equipment, with a significant cost reduction related to these processes.
The choice of solutions based on standard architectures and protocols allows integration with the majority of the WMS (Warehouse Management Systems) and WES (Warehouse Execution Systems) on the market. The integration enables an intelligent management of the warehouse and all processes within it.