Optimization of handling activities in air cargo areas
Efficient and safe management of cargo loading/unloading activities by locating trucks and towed vehicles used for transporting containers
To manage cargo loading and unloading operations effectively and safely, Ubiquicom has proposed a solution that uses a combination of technologies (satellite and proximity) and location logic (direct and indirect) to find the trucks and trailers used to move containers.
THE CUSTOMER
The customer is one of the global leaders in the logistics and transportation industries. In business for over 50 years, its divisions handle more than a billion packages per year and employ more than 300,000 employees on five continents, covering requests from all industries.
THE REQUIREMENTS
The customer requires monitoring the location of hundreds of towed vehicles (mainly dolly pallets) and dozens of trucks within the cargo area of a large Italian international airport hub. The area of interest stretches across all the outdoor areas of the terminal and the flight side, totaling an area of more than 10 square kilometers.
The operators responsible for coordinating the loading and unloading of cargo aircraft require knowing in real time the position and status of each individual truck. It is also important to give workers authorization to drive vehicles with a centralized access control system and compile historical data on the routes taken and how to use the fleet.
The towed vehicles are handled exclusively by trucks, but once released, they often remain isolated in remote areas or are mistakenly picked up and used by others operating in the area. A large part of these assets consists of special trolleys (dolly pallets) for the transport of containers and aircraft pallets. To improve operation management, it is important to know not only the position but also the load status of the trolley (present load or absent load).
Collecting data on dolly usage (hours of use, mileage, number of loading or unloading operations performed, etc.) is invaluable in helping plan their maintenance and make sure the right size is in circulation in a timely manner.
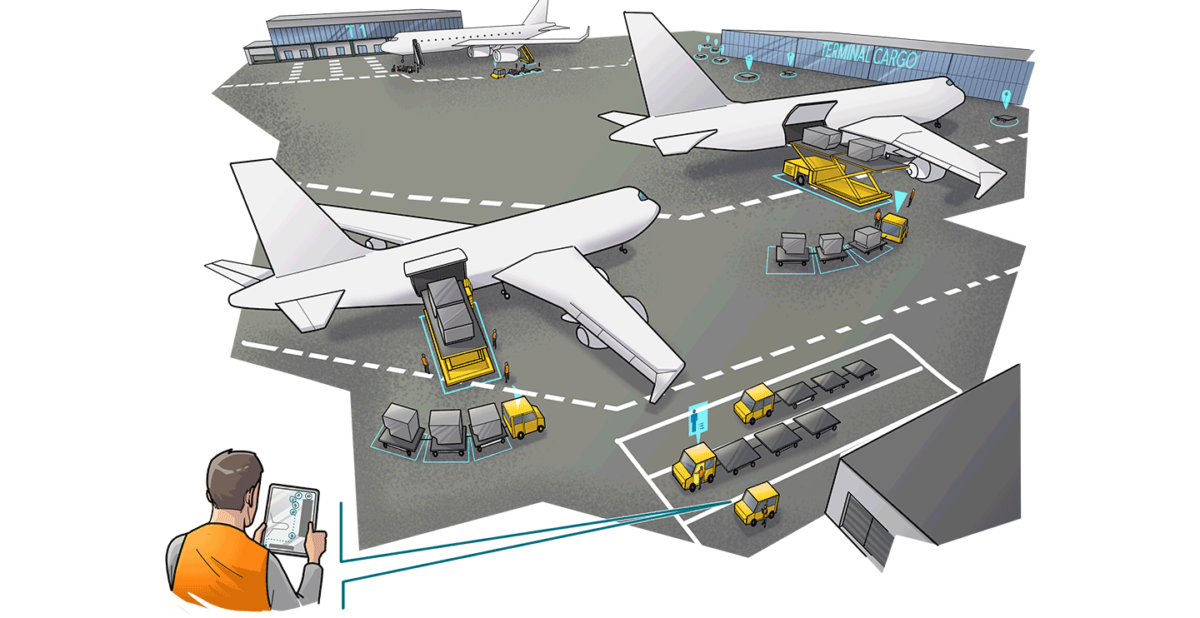
THE SOLUTION
Ubiquicom has presented a solution consisting of combined technologies (satellite and proximity) and locating processes (direct and indirect) to address all functional and undefined needs.
The project has presented new technological, energy, mechanical, and electrical challenges that have been overcome due to the know-how created by Ubiquicom in the fields of asset tracking and industrial IoT.
The solution specifically uses GNSS and BLE technologies to pinpoint the location of trucks and trailed vehicles, using both direct and indirect location approaches to ensure the project is energy efficient and can last without needing to replace or recharge batteries beyond the regular maintenance cycles provided for trolleys.
The coordinated use of different Ubiquicom systems was necessary to meet different requirements at the same time.
- TrackVision – the cloud-based solution for telemetry and remote control,
- Locator – the locating platform and IoT,
- Forklift Companion – the vehicle terminal integrated with Ubiquicom solutions;
- BLE sensors and multi-technology low-consumption tags.
Through the Ubiquicom Locator and TrackVision, enabled users can:
- Monitor the location of the trucks and trailers and their status (free or loaded).
- Consult historical data, reports, and analysis tools.
Administrators can instead:
- Configure zones;
- Enable individual operators to use vehicles;
- Define rules, events, and alarms;
- Arrange the generation and sending of periodic reports;
- Check the usage status of each truck and trailer.
The platform APIs also allow integration with other software platforms. The Forklift Companion vehicle terminal, mounted on the trucks, displays the dolly position with the status (free or loaded) in order to allow drivers to identify the necessary resources and reduce search times. The same terminal is used for access control, the operational checklist, the reception of the assigned mission (with a display on the origin map), and the destination of the transport.
RESULTS
The customer achieved the following results:
- Periodic reports on the use of trucks and towed vehicles (working hours, kilometers, rate of use, impacts, login/logout number, etc.) to support maintenance teams;
- Real-time visibility of the location and status of the truck fleet from the control room and managers’ terminals;
- Better orchestration of the operations of assignment of the task to the single vehicle, minimizing the superfluous interactions and, therefore, the times of execution;
- Visibility of the position and status of the towed fleet both from the control room and for the truck drivers; reduction of the search time; optimization of the rate of use of the resources for greater efficiency;
- Reduction of total handling times (loading and unloading);
- Possibility of retrospective analysis of operating flows to further optimize operations;
- Control the use of the fleet and the related permits;
- Increased security thanks to:
- access control
- less kilometers without a load on dollies
- pre-operational checklist
- the ability to slow down or limit the movement of vehicles in critical areas (also depending on the time and day).
CONTACT US
CASE STUDIES
Over the years Ubiquicom has helped numerous companies improve their corporate processes, reduce management costs and increase efficiency.
Discover which companies have taken advantage of Ubiquicom’s know-how to improve their productivity!
«Smart integration» of machinery and data for process optimization: iDAC
A suite of tools and services for data-driven fleet management of cleaning equipment