Asset tracking to reduce costs in the industrial sector
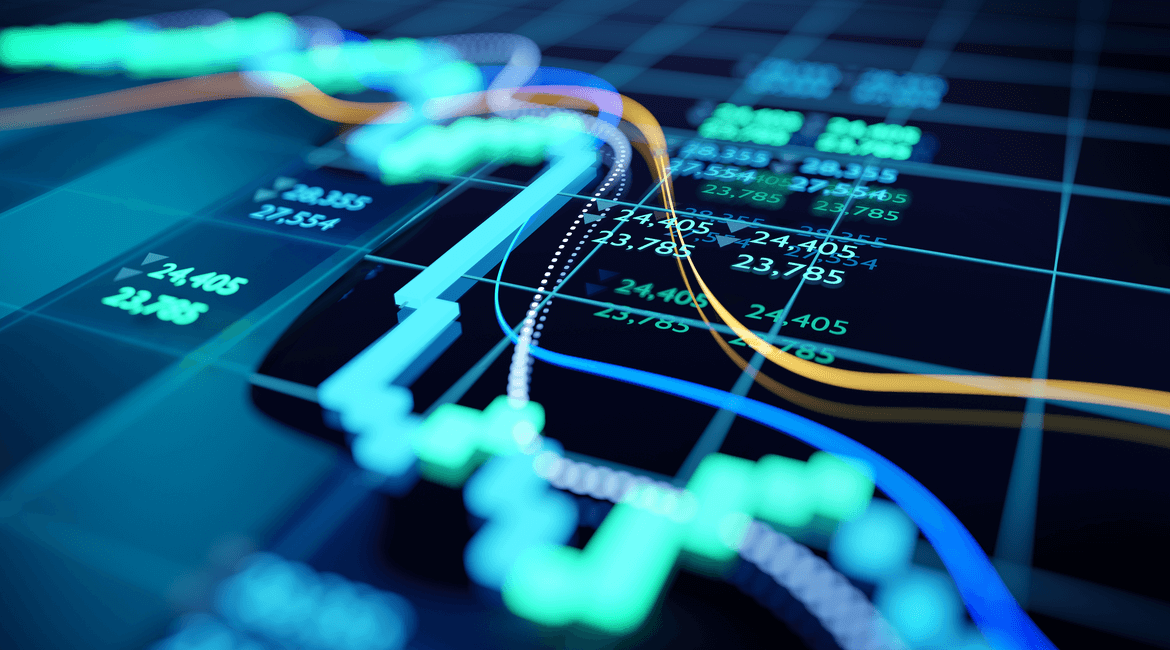
Indipendently from industries and leading sectors, the use of asset tracking allows companies to benefit from various advantages.
Among these, there is one cost reduction related both to the operations that take place within production and warehouse areas, as well as activities strictly related to asset management.
From the optimization of the management of vehicles and machinery, to compliance with industry regulations, to the efficiency of all production and warehouse processes: the use of location and tracking technologies and systems allows to save time and costs, and direct the company’s resources where they are really needed.
The end of the time lost looking for equipment thanks to asset tracking technologies
Even today, many companies rely on anything but precise procedures to monitor assets. Sometimes, even control of work equipment, semi-finished products and goods essential to logistics operations is performed by sight from workers. Manual asset monitoring is not efficient and can require considerable effort, as well as often being unreliable.
These inefficiencies have a high cost for companies. Workers spend valuable time searching for assets, such as goods or semi-finished products, time that could be redirected to more important processes.
An approach based on Industry 4.0 technologies, such as Artificial Intelligence (AI) and Industrial IoT (IIoT), allows instead to correct these critical issues and, therefore, save time and costs. This is possible, for example, thanks to RTLS systems (Real-Time Locating Systems). These systems consist of software tracking platforms connected with location IoT devices mounted on assets or supplied to workers. Thanks to these technologies, the company can easily improve the efficiency of processes and increase productivity.
By taking advantage of technologies such as UWB (Ultra Wide-Band), BLE (Bluetooth Low Energy) and Wi-Fi, RTLS can achieve very high precision and high accuracy. Thanks to these technologies, RTLS systems identify the location of the vehicles used for material handling processes within production and storage areas. In addition, starting from this tracking activity, they are able to also provide the location of the goods themselves.
A possibility that allows the company to immediately have access to the current position of the asset and easily direct the worker.
Improving inventory management
The use of systems for indirect localization of goods (finished products, but also semi-finished products for production) also allows the company to optimize inventory management.
For example, it makes possible a more efficient management of supplies, reducing the risk of being left without essential components for production. This high level of visibility – attainable thanks to the use of UWB technology- translates into competitive advantages also for logistics companies.
The automation of inventory management allows, in fact, to reduce human error, among the first causes of fulfillment problems within inventory management. For example, according to a recent survey, the stock out of a product that has been ordered is the main management error that can be made in this area and the reason that most often leads to the loss of customers. Automation allows to avoid running into this type of situation.
Safe operations and compliance with industry regulations
Another area in which the use of asset tracking systems helps companies reduce costs is that of safety. Thanks to specific functions provided by some RTLS solutions, it’s possible to limit the use of vehicles only to workers who have the required skills and certifications.
At the same time, it’s possible to limit access to critical areas of the facility, without the need to implement the presence of physical barriers. In this way, the company can be sure that the performed operations are in compliance with industry safety standards.
In addition: the reduction of the risk of accidents for an organization also translates into prevention of sudden stops to operations, that would involve very high costs.
Reduction of maintenance costs with asset tracking systems
RTLS systems, thanks to the bidirectional communication between devices installed on board the vehicle and software platforms, allow to collect important information on the vehicles used. Information – such as battery status, fuel level, engine temperature-that create the possibility to monitor in real-time the status of assets and that, thanks to tracking platforms, can be collected and controlled over time. This allows the company, for example, to promptly detect the malfunction of a vehicle and take action before any malfunction occurs.
The use of an asset tracking platform enables, therefore, a more efficient maintenance management. Thanks to the history of the actions conducted and the data relating to the performance of the vehicle, the organization can schedule actions when they are actually needed.
Enabling predictive maintenance allows the company to cut significant costs. Taking action only after a malfunction, in fact, puts operational continuity at risk. However, planning actions regularly regardless of specific needs is also a waste of resources.
Lower costs thanks to asset tracking systems
The use of RTLS systems and asset tracking platforms, in contrast, allows the company to implement a condition-based maintenance.
The high visibility of operations and all company assets – workers, vehicles and goods – makes it possible, therefore, to cut unnecessary costs and avoid waste. A truly smart asset management frees important resources, which can be used to increase productivity and competitiveness of the company.
RTLS systems are crucial for improving operational efficiency in many sectors and on many occurences, discover all the use cases and some of our success stories
Want to learn more?
Fill out the form, and an our expert will contact you for further information.