Smart logistics partner: why choose Ubiquicom for your projects
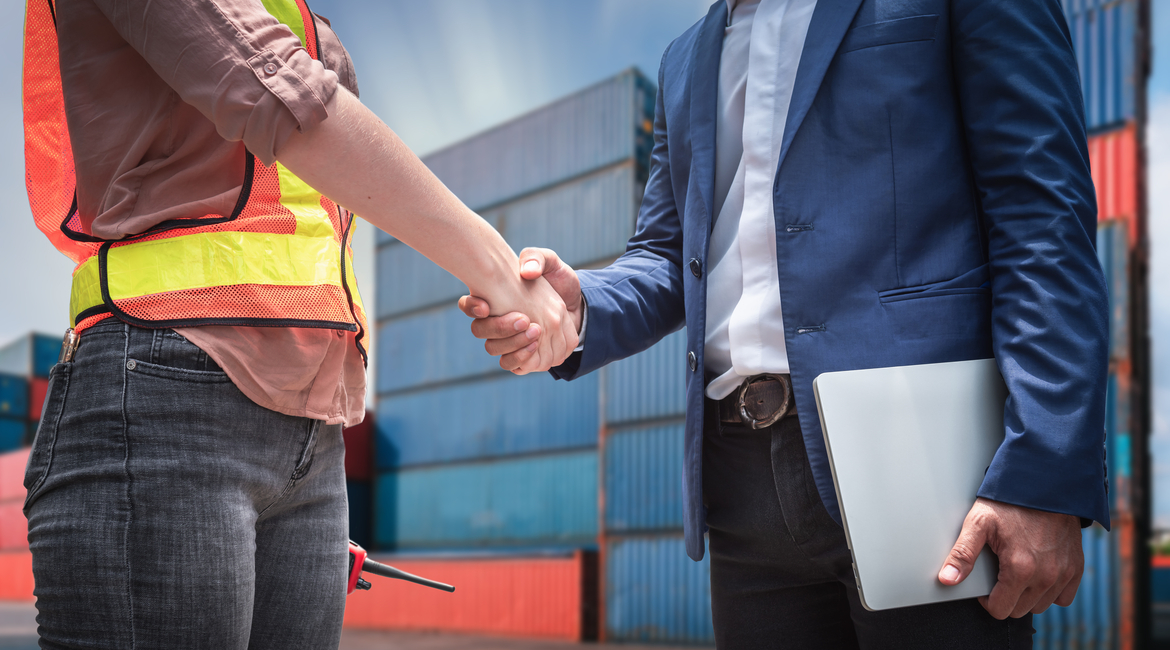
Disruptions in the supply chain, with difficulties in supply and the rise of prices of raw materials and energy, lead companies to smartly manage both stock and processes. Although these difficulties have already come to light during the pandemic, data shows that, to this day, only 6% of companies have complete visibility across the supply chain.
Real-time localization and tracking systems (RTLS, Real-Time Locating Systems) can help companies achieve greater visibility in internal processes – such as inventory management, material handling equipment tracking and warehouse task planning – and throughout the supply chain.
Logistics partner: why choose Ubiquicom
With its innovative localization and tracking solutions, Ubiquicom is able to offer customers a portfolio of smart logistics tools capable of providing companies a more efficient process management.
Thanks to the great experience in the integration of all localization technologies and systems – UWB (Ultra-wideband), BLE (Bluetooth Low Energy), GNSS (Global Navigation Satellite System), and GPS (Global Positioning System) – with its own innovative software Locator, Ubiquicom can adapt and reshape its offers based on the needs of each company in the Safety & Efficiency areas.
From direct tracking of vehicles, people and goods, to AI-based technologies meant to make all warehouse operations efficient, Ubiquicom’s offer is designed to give maximum visibility throughout the supply chain.
Efficient warehouse management with RTLS and AI
In the warehouse, processes and assets are not always managed efficiently. Many companies, for example, rely on visual control to identify goods and vehicles for material handling operations or for planning tasks. This is an approach that leaves room for human error and puts workers in activities that today can be performed more quickly and efficiently using technologies.
A WMS (Warehouse Management System) already allows companies to manage warehouse processes in a smart way. Integrating this with a location and tracking platform is a further step in the efficiency of processes and resources, and in cost reduction. Hardware and Ubiquicom platforms for indoor and outdoor tracking of material handling vehicles address these needs. At the heart of the company’s offer is the Locator Suite, a Real-Time Locating System (RTLS) that optimizes the functionality of resources and offers support to decision-making processes in the logistics field through Big Data and IoT.
Integrated with SYNCHRO – solution that combines tracking technologies, such as RTLS and artificial intelligence (AI) – the Locator Suite grants efficient management of all warehouse activities, starting with material handling processes. Thanks to standard architectures and protocols, SYNCHRO can be integrated with most of the WMS on the market.
The integration with Locator Suite allows SYNCHRO to check the progress of tasks and manage any mismatches (delays or advances) of the planned activity.
AI algorithms allow the optimization of task sequence based on available resources. In this way, inefficiencies, time and costs of operations are lowered, thanks to the reduction of transfer routes between one task and another and of movements involving forks without loads.
Safer operations: why choose Ubiquicom as your smart logistics partner
In intensive processes such as the ones in logistics, companies need to speed up operations while maintaining high levels of safety. To meet these needs, Ubiquicom has developed advanced anti-collision systems, such as Proximity.
Proximity helps companies to drastically reduce accidents between forklifts or other vehicles and people. The solution takes advantage of Ultra-wideband (UWB) technology to measure the distance between two vehicles or between a vehicle and a worker. The highly accurate measurement is a result of radars mounted onboard the truck and tags assigned to the staff.
Proximity, however, goes beyond identifying and reporting dangerous situations: in fact, it also allows companies to automatically implement actions that prevent collisions, such as slowing down the vehicle.
Improving safety management without physical barriers
Thanks to the software, the company can create reports of accidents that occurred and that almost did (near-miss events) and implement strategies to improve safety. For instance, companies can set slowdown zones near dangerous or particularly busy areas through the software.
It is possible to do this quickly and easily, without implementing physical barriers in the area. In addition, the intuitive software allows users to redesign these areas very easily and in real time, promptly responding to the needs of the warehouse.
Thanks to Ubiquicom’s commitment to continuously innovate its offer, companies can now enjoy the benefits of Proximity with new features connected to vehicle localization using BlueBox, Ubiquicom’s device for tracking and telemetry of vehicles and motorized assets. With the integration of Proximity, which creates a “safety bubble” around vehicles and people, it is possible to define risk zones, track near-miss events, highlight stationary obstacles, using the localization of the vehicle itself.
Indirect localization for a real-time control of the warehouse stock
Packaging and delivery of wrong products are the causes of 17% of inventory errors leading to customer loss. For this reason, the need for speed in logistics operations goes hand in hand with accuracy.
In this scenario, localization technologies are useful to know the location of goods within the warehouse or in production environments. When the volumes are too high or the unit value of the product is low, one can resort to indirect localization, which enables a greater visibility of the stock. The applications of this solution can be found in all cases involving large warehouses, even outdoors, where the goods are stacked in yards. Even finished and semi-finished products are large, often also arranged in stacks of two or more levels (e.g., coils, bars, beams, tubes, sheets and so on).
Ubiquicom’s solutions take advantage of different localization technologies: on-board devices, UWB infrastructure, Locator licenses. These are complemented with RFId readers on the forks – or a barcode reader supplied to the forklift driver – and a fork height sensor for each vehicle.
Given a defined area, this shows the position of the products, providing a visibility that allows a better control of the stock and faster movements.
Logistics partner: yard management solutions
Warehouses are complex structures where each area has specific needs and risks associated with. The introduction of material handling technologies allows, on one hand, to free workers from repetitive and dangerous tasks. On the other, the use of autonomous vehicles and robots for material handling operations introduces new challenges to personnel safety, especially when vehicles and workers coexist in the same area.
Ubiquicom helps customers achieve efficiency not only in indoor areas, but also in the yard management. Loading and unloading areas can be very extensive and, in many cases, the operation management is still done manually. This is a strategy that is not very efficient, because it leaves room for human errors in areas that are very busy, with the presence of heavy vehicles and operators.
Ubiquicom’s solutions for yard management take advantage of tags equipped with a viewer, assigned to the vehicle which is being tracked. At the same time, the viewer allows the driver to view the necessary information to load and unload the products.
Direct tracking: how it works and when it’s instrumental
The software and devices developed by Ubiquicom can be used in numerous industries and applications.
The value of tracking solutions extends beyond the boundaries of the warehouse. In some cases, it may be necessary to track goods along the delivery route to protect them and their quality.
This is useful for goods that have a high value per unit, such as luxury products and works of art. In this case, the localization is done through tags that use data network (SIM) and that can be hooked to any network in the world. Thanks to these tags and GPS technology, it is possible to follow the product delivery in real time.
The company is thus able to ensure that the products actually arrive at their destination and can accurately estimate waiting times, improving customer service.
Direct tracking, other areas of application
Tags for direct tracking of goods also provide useful information to control the quality of products, such as temperature, acceleration, and shock suffered during transport.
This information is particularly effective in the transport of food and beverage or fragile products. To meet these needs, Ubiquicom’s offer includes certified devices for food that can track the cold chain with great accuracy.
In this case, it is not necessary that the information is updated in real time, but it is sufficient that it is available at the time of delivery.
By choosing Ubiquicom as a logistics partner, companies will therefore be able to rely on innovative technologies and a personalized approach. Thanks to the experience of the Ubiquicom team, customers are followed by professionals able to develop a customized project, selecting the technologies and systems that best meet their specific needs within a logistics 4.0 perspective.
Want to learn more?
Fill out the form, and an our expert will contact you for further information.