Warehouse logistics: IoT, RTLS and AI to support WMS
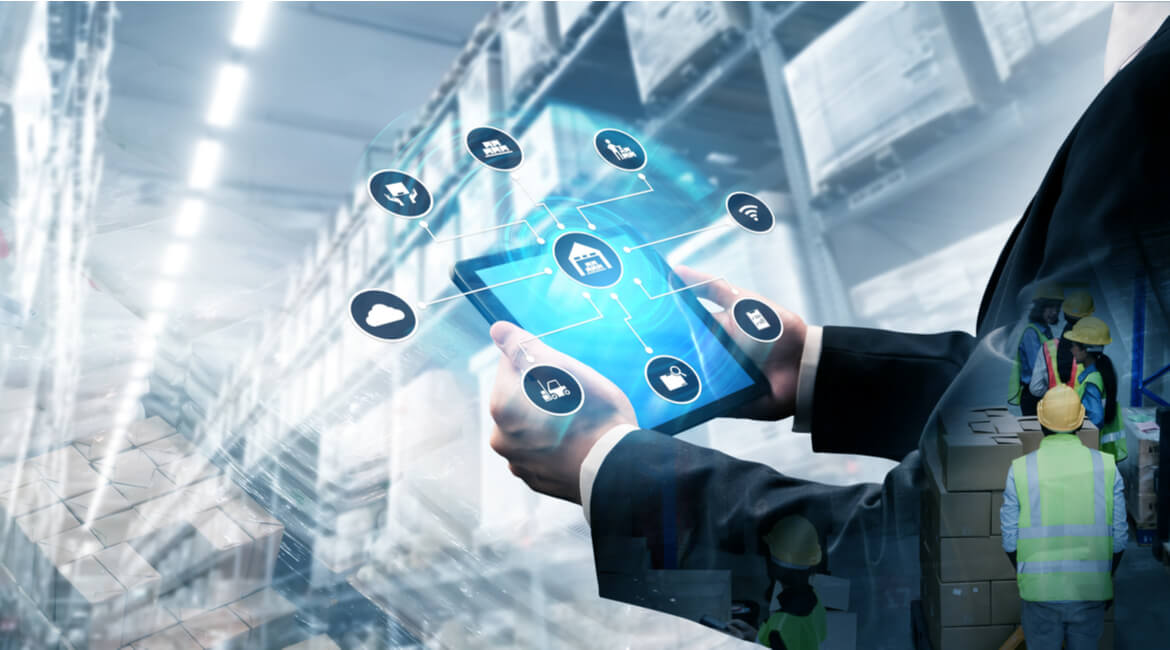
The use of Industry 4.0 technologies is deeply transforming warehouse logistics. The ability to connect assets used in logistics processes (such as material handling vehicles), thanks to the Internet of Things (IoT), allows more efficient operations.
Operations in logistics 4.0 become more and more automated. On one hand, this automation makes it possible to speed up actions, relieving workers of those dangerous or repetitive tasks with low cognitive value.
On the other hand, the introduction of autonomous vehicles into warehouses also transforms these settings into hybrid spaces and requires special focus on the safety of workers.
Hence the need for increased visibility on the entire supply chain of a company. A visibility today possible thanks to the integration of IoT and Artificial Intelligence (AI) with company resources, such as ERP and WMS.
IoT in the service of warehouse logistics
Logistics companies find themselves having to face a number of challenges today. The growth of e-Commerce demands faster delivery times in consideration of reductions in profit margins (with many platforms offering free shipping).
Moreover, in addition to the product, consumers today pay more and more attention to the service, which must live up to their expectations. It is sufficient to think that packaging and delivery errors represent the 17% of malfunctions in inventory management leading to loss of customers.
A warehouse must therefore be a machine that works perfectly, where downtime must be reduced to zero and all processes must be managed with greater efficiency.
Integration of IoT and RTLS with WMS: benefits of asset tracking
The introduction of IoT in these contexts allows data to be collected, in real time, on the vehicles used for material handling operations and on the goods.
RTLS systems (Real-Time Locating Systems) are composed by hardware devices installed on board of vehicles. They communicate with software platforms for localization and tracking and they allow to monitor the position of vehicles used in material handling processes.
Communication is enabled by technologies such as BLE and UWB, depending on the level of precision required in detection and on the context.
RTLS systems are very versatile and can generate great benefits and efficiency in various contexts.
An example can be found in intensive logistics where assets localization, combined with the use of AI applications and integration with systems such as WMS enables serious benefits.
Warehouse logistics, how to reduce empty miles with IoT, RTLS and AI
For example, in this case this integration allows to minimize execution times of tasks and empty miles, enabling a reduction in total operating costs of 15-25%.
Integration of RTLS systems with WMS in fact, allows to build simulation models that ensure a better planning of resources.
Models built using data take into account possible variations in the execution of tasks (number of carts used) in comparison to several shifts, days and seasons. The model takes into account other important information as well, such as routes of carts, lead time, traffic data, and bottlenecks.
The simulation with exact calculations per minute gives the company an indication of the reduction of costs that could be achieved. A reduction that results from higher speed in operations, with the use of equal resources, therefore from a minimization of necessary trips and empty miles. Or, by increasing saturation of carts, so that the company can reduce the number of carts necessary for the tasks.
Greater visibility thanks to indirect tracking of goods
The reduction of operating costs also involves greater efficiency in the management of semi-finished and finished products. A particularly relevant necessity in those production contexts characterized by large volumes, such as the manufacturing sector, production and large logistics hubs.
Through RTLS systems of indirect localization, it is possible to remove human error and enable efficient control of stocks, thanks to reduction of search times.
Integration with WMS provides a really smart management of products and also of semi-finished products available in the warehouse.
Better inventory management
This integration enables a smarter inventory management. In addition to cargo handling times – that in these contexts represent a substantial part of the operations – errors are also reduced.
Thanks to data provided by IoT sensors, in fact, WMS can monitor all information on the warehouse inventory, such as the minimum thresholds of stock levels. There’s more: the system is also able to automate orders of products, reducing the possibility of being left without raw materials or finished products.
In addition, thanks to the use of AI algorithms, the company can improve inventory positioning, taking into account the necessities of the warehouse.
More efficient warehouses thanks to WMS, IoT, RTLS and AI
The real time control of material handling equipment also enables to redistribute tasks according to contingent situations This allows fairer workloads among company resources, it avoids overwork for individual employees and reduces the possibility of error.
In addition, the analysis of on-site collected data also helps to improve safety in production and inventory areas. An example comes from the analysis of transit data of vehicles in various areas and of accidents nearly occurred (near miss) between forklifts or between forklifts and people. Analysis that is able to identify critical areas inside the warehouse or production facility.
Valuable information that allows the company to intervene promptly by enhancing workers and vehicles safety. Again in this instance, greater efficiency is enabled through elimination of critical issues and bottlenecks.
How warehouse design can change in logistics 4.0
The use of IoT and Artificial Intelligence makes it possible to create a digital model of a warehouse, experimenting with re-design strategies of spaces in a virtual setting before implementing them in a real space.
This allows the company to reconsider spaces according to their needs, reducing the times and above all the costs of these operations. In this way, companies can create “future-proof” warehouses, meant to evolve with the business.